In the transport industry, ensuring that cargo remains securely restrained is a fundamental aspect of road safety. You’re either going to use direct restraint (e.g. locking a container to a skeletal truck), or indirect restraint (lashings over the cargo that pull it down onto the deck). The latter relies somewhat on friction to help.
The science of load friction plays a critical role in determining how effectively a load remains stable during transit. Friction influences how loads interact with the vehicle deck and securing mechanisms such as tie-down lashings, straps, and chains. A clear understanding of frictional forces allows drivers and logistics professionals to mitigate risks associated with shifting loads, ultimately reducing accidents and damage to goods.
Understanding Friction in Load Restraint
Friction is the resistance to movement between two surfaces in contact. In transportation, this resistance is a crucial factor in maintaining load stability. The force of friction depends on two primary elements: the nature of the contact surfaces and the force pressing them together. Contrary to common belief, the surface area of contact does not significantly impact friction; rather, it is the combination of surface type and normal force that determines frictional resistance.
Friction in load restraint is divided into two categories:
- Static friction: The force that prevents an object from starting to move.
- Dynamic friction: The force resisting movement once motion has begun.
For transportation safety, high static friction is preferred because it provides resistance against initial load movement. If the static friction is overcome, the load may begin to shift, leading to potential instability.
Factors Influencing Load Friction
Several factors affect friction levels between the load and the vehicle deck, influencing how effectively a load remains restrained during transport:
- Surface Material: Different materials exhibit varying levels of friction. For instance:
- Wet or greasy steel-on-steel surfaces have very low friction.
- Smooth steel-on-timber surfaces have medium friction.
- Rubber load mats on steel decks provide high friction.
- Load Weight and Clamping Force: The downward force exerted by the load and any applied tie-down tension influences friction. Clamping force, created by tie-down lashings, enhances load restraint by increasing the force pressing the load onto the vehicle deck.
- External Contaminants: Oil, water, dust, or sand between surfaces can significantly reduce friction, increasing the likelihood of load movement.
- Anti-Slip Measures: Friction can be enhanced by using rubber load mats, dunnage (such as timber spacers), or interlayer packing to improve grip between surfaces.
Load Restraint Methods and Friction
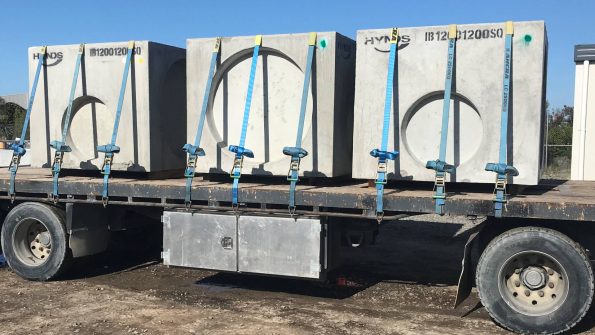
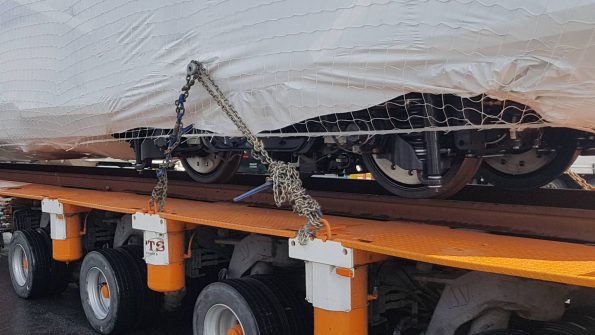
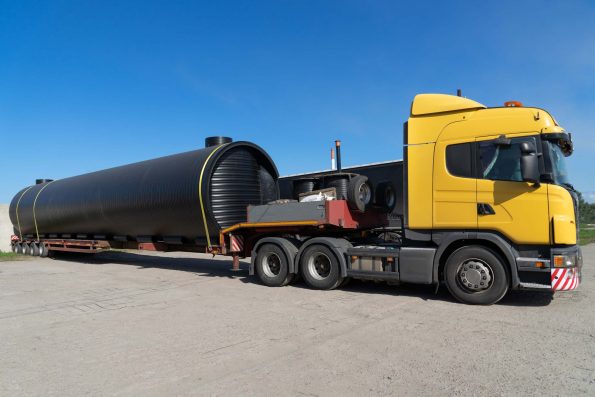
Different load restraint techniques rely on friction as a primary or supplementary factor in securing cargo:
- Tie-Down Restraint: This method uses lashings, such as webbing straps or chains, to clamp the load to the vehicle deck. The effectiveness of tie-down restraint depends on the friction level between the load and the deck. Higher friction reduces the number of lashings required, whereas low-friction surfaces necessitate additional tensioning.
- Blocking and Containment: Some loads are physically blocked using vehicle structures, such as headboards or side walls, reducing reliance on friction. Contained loads, such as bulk goods inside a rigid container, rely less on surface friction but still benefit from a high-friction base to prevent internal shifting and pushing against the containment devices.
- Direct Restraint: This method restrains the load by attaching it directly to the vehicle’s body or frame, minimising movement without depending on friction. An example would be chaining a wheel loader to a transporter trailer.
Calculating Friction and Load Stability
In transport operations, understanding the friction coefficient (μ) is vital in designing an effective load restraint system. The coefficient of friction varies depending on material combinations. Some typical values include:
- Wet or greasy steel-on-steel: 0.01–0.1 (very low friction)
- Smooth steel-on-smooth steel: 0.1–0.2 (low friction)
- Smooth steel-on-rusty steel: 0.2–0.4 (low to medium friction)
- Smooth steel-on-timber: 0.3–0.4 (medium friction)
- Rusty steel-on-timber: 0.6–0.7 (high friction)
- Smooth steel-on-rubber load mat: 0.6–0.7 (high friction)
The pre-tensioning of lashings also affects the load’s overall stability. For example, a properly tensioned 50 mm webbing strap using a hand ratchet may achieve a pre-tension of 300 kgf, significantly increasing clamping force and frictional resistance.
Best Practices for Maximising Load Friction
To enhance load stability and improve transport safety, consider the following best practices:
- Use High-Friction Materials: Placing anti-slip rubber mats or timber dunnage under loads can significantly increase friction.
- Apply Adequate Pre-Tension: Ensure tie-down lashings are correctly tensioned to enhance clamping force, preventing load shifts.
- Keep Surfaces Clean: Remove oil, grease, or debris from surfaces to maintain high friction levels.
- Secure Load Evenly: Distribute lashings and securing mechanisms evenly to maintain consistent friction across the load.
- Regularly Inspect and Adjust Restraints: Check lashings and adjust tension periodically, especially during long journeys where vibrations may loosen restraints.
Conclusion
The role of friction in load restraint is fundamental to safe and efficient transport operations. Understanding how friction interacts with surface materials, weight distribution, and tie-down methods ensures that loads remain secure throughout transit. By implementing best practices such as using high-friction surfaces, applying appropriate clamping force, and conducting regular restraint inspections, transport operators can significantly reduce the risks associated with shifting loads. Proper friction management not only ensures compliance with load restraint regulations but also enhances road safety for all users.