A shipping container is a convenient, standardised size that makes it easy for intermodal transport – they can be loaded straight from a ship to the back of a truck without devanning (removing goods from a sealed container). This means that a container can be sealed at source and not opened until it gets to its destination, which is good for security and to verify a load hasn’t been tampered with.
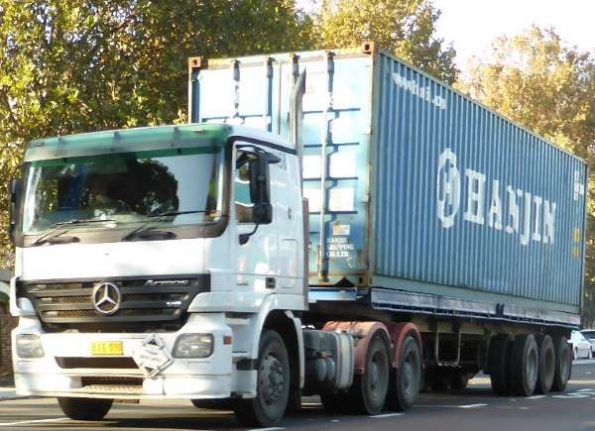
However, there are issues that truck drivers need to be aware of when transporting shipping containers.
ISO twistlocks
By far the best way to secure a shipping container to a truck is to use the four ISO twistlocks on each corner. These are cast metal locks that fit into four slots. Using a handle on each one, the driver locks the container to the truck or trailer’s flat deck or chassis (in the case of a skeletal trailer). However, it does require that the driver locks them, otherwise the container can roll off the trailer.
Skeletal trailers, or ‘skels’ are available in different configurations for different sized containers.
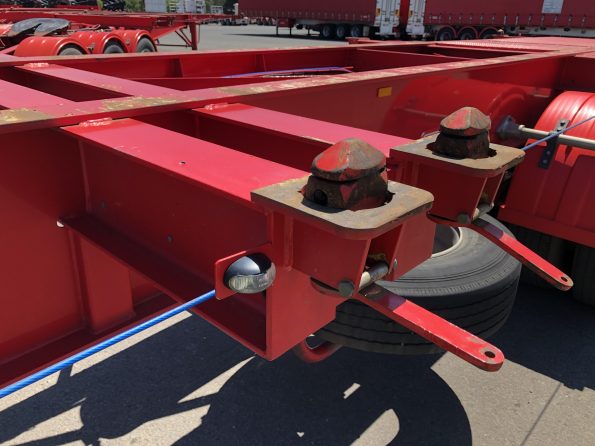
An alternative to using ISO locks is attaching the container using chains. This is not ideal as chains are harder to manage and there’s more risk of the load not being secured correctly. An ISO lock secures the container to the truck, therefore, at minimum, the mass of the container functions as part of the truck. The issue is then with the contents.
Loading a container onto a truck
Once the container arrives, for example on a ship or train, it has to be placed on the semiskel. The transportation of containers is a massive and fast-moving industry, so specialist materials handling machines help quickly and accurately place the containers on the truck.
Large cranes remove the containers from the ship. They are capable of lifting containers straight onto and off the trucks.
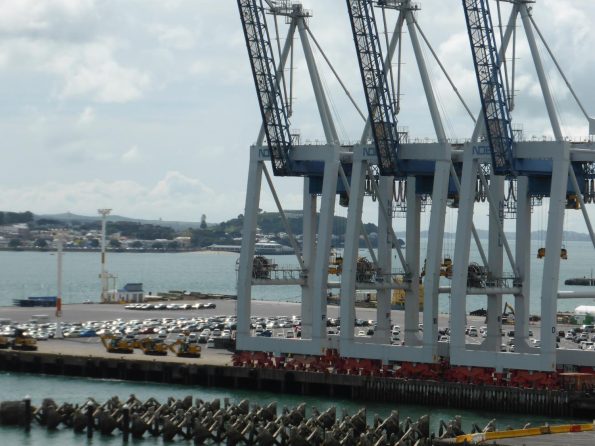
Straddle carriers move containers around a port or container yard and can ‘straddle’ a truck and lower the container onto it.
Reach stackers can reach containers off high stacks and place them on the truck.
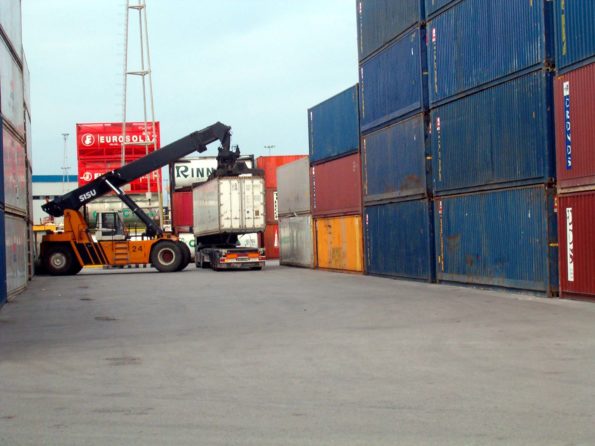
Forklifts use the fork pockets at the base of the container and can lift them and travel with them to the truck’s location.
Combilifts – a kind of mobile gantry crane – are designed to remove one container from a truck and take it somewhere else in a yard
A truck might also have a side loader where it can load the container itself using two small cranes attached to the trailer chassis.
Centre of gravity
When a flat deck, reefer or curtainsider is loaded, the driver can see what’s being carried and make an estimation of where the load’s centre of gravity is. They can load (or instruct the loader) to make adjustments to shift the weight forwards or backwards to help with axle loadings. However, as containers are sealed, it’s not possible for a driver to know how a container has been loaded, or even that the contents haven’t moved or are rolling around freely.
A loose load will develop its own kinetic energy, banging against the sides of the container and adding forces that will destabilise it when cornering and braking.
A weighbridge (or a modern side loader) can help with distributing the load correctly over the axles, but there’s no way of knowing how high the centre of gravity is within the container itself. The higher the centre of gravity, the more easily the truck will roll. In some cases, the truck might exceed the recommended static roll threshold.
Overweight containers
It’s estimated that some trucks carry containers are overloaded. This is due to misreporting of weights on shipping documents, meaning that they are placed onto trucks that are not suitable for the load. Unfortunately, the driver is the one responsible for the load and therefore can be fined if the truck is overweight. The only way to tell if the truck is overloaded is to go to a weighbridge, which takes time and costs money. The driver should be able to assume that a shipping container’s documentation is accurate.